Company Activity
At Jones, we recognise the growing awareness around the demand for responsible business behaviour with issues relating to sustainability, ethics and respect for all of our stakeholders. We are extremely passionate about culture, diversity and inclusiveness in the workplace and recognise the impacts that they have on both their environment and the society in which they operate.
Filter posts by category
JEG Specialist Lift Division
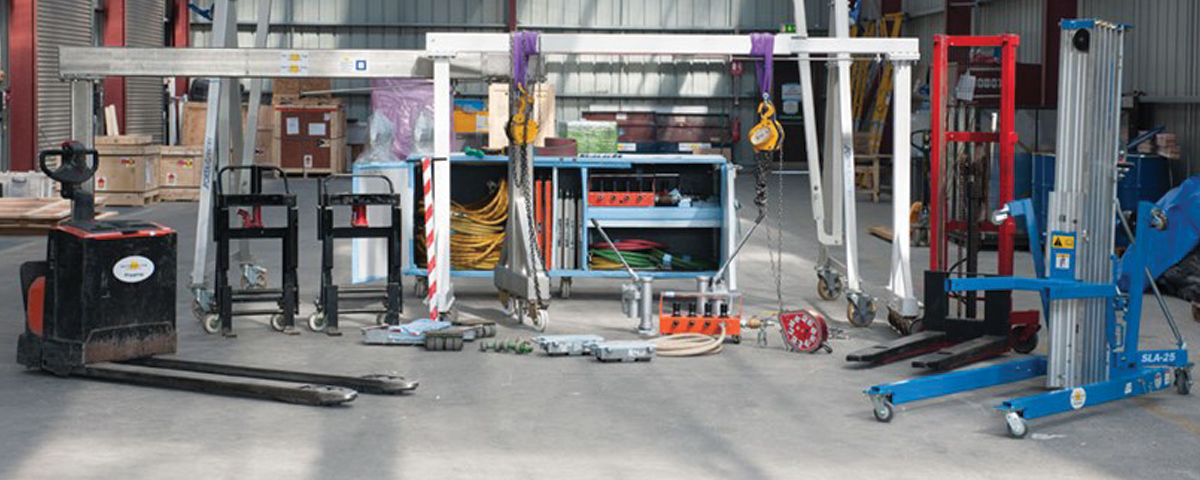
In this issue of LEAN Times we look into the Jones Engineering Group highly efficient and highly experienced Rigging Department. We look at what they do, how they do it and what they use. We also examine the Inspection and Testing side of the division and get some insight into how testing and inspections are carried out. In our on-line publication we talk to Bob Hatfield, Senior Inspections Supervisor about inspections and testing.
Jones Engineering Group Specialist Lift Division specialises in the lifting, installation and relocation of plant and equipment. This also includes a qualified Testing and Inspection Division. Our Specialist Lift Division, (S.L.D.), has established and successfully delivered these services for many of the leading multinational manufacturing companies both here in Ireland and further afield. Our work involves the additional complexity of undertaking these services in live operational facility environments where safety and attention to live services and impact to the customer is paramount. A critical facet in delivering a high performance service is our commitment to safety. We believe in the highest degree of planning, and safety is set at the maximum level.
From a single equipment move to complete factory relocation, our Specialist Lift Division has the solution. This division of the company is made up of highly trained and experienced rigging crews with a broad range of mechanical engineering skills that specialises in the handling of everything from the smallest most sensitive equipment to heavy industrial plant
Overview of the S.L.D. By various SLD team members
Some of the equipment we deal with is often very complex and is frequently vibration sensitive while some are temperature controlled. This has driven us to develop specific rigging installation procedures over the course of our past projects to meet these demanding and ever-changing conditions.
The equipment ranges in value, size and complexity, with some plant weighing as much as 50 tonnes and costing several millions.
Bespoke Lifting Equipment
On several occasions the need has arisen to design and fabricate bespoke lifting rigs and set-ups for specific tasks. This has given us the advantage of being able to take on any task. Here is an example of such an occasion: This 10T Roller Bed Frame (pictured above) was designed and fabricated to facilitate the unloading of certain temperature controlled equipment that arrives in 5no 40ft temperature controlled air freight trailers. The roller bed acts as an extension to the trailer and allows us to unload the equipment safely and also reduces the amount of man hours by approx. 75%. It also minimises the duration that the equipment is open to the elements.
5t Lifting/Transportation Table
A 4.5t motor was required to be de-installed from a compressor as part of an upgrade project. The compressor needed to be de-installed electrically & mechanically and the compressor moved off its plinth in order for the motor to be lifted out using A-frames or a forklift depending on congestion in the area. The client’s on-site vendor was contracted to de-install the roof and other sections of the compressor housing to allow the motor to be removed easily. This task put the client at risk as the compressors in the area are all electrically linked and by taking one out of the system all are out of the system. This meant to de-install and lift out the motor, the compressor down time was approx. one week. We designed and fabricated a 5t lifting table that can be assembled to one side of the compressor which allows the motor to be de-installed from the compressor in-situ.
A mechanical aid is attached to the table which supports the transfer of the motor both onto and off the table. Once complete the table can travel on its own castors with the motor safely secured to a required loading/unloading destination. This has reduced the cost significantly by eliminating mechanical, electrical 3rd party costs and down time of the compressor for the customer by 50%
Test & Inspection Division of the S.L.D.
Jones Engineering Group has an in-house Testing & Inspection Division that specialises in inspecting and certification of lifting equipment. The crew are trained members of the Lifting Equipment Engineers Association (LEEA). The (LEEA) is established across
the globe as the leading representative body for all those involved in the lifting industry worldwide. Our mobile crew service the country for all JEG projects directly and also 3rd party customers. Periodical inspections and testing is carried out on all types of lifting accessories and appliances.
We also advise clients on the type of equipment that would be suitable and practical for them and we can also fabricate bespoke lifting attachments to suit the needs of the client. Repairs and servicing of equipment is also catered for.
What do we do?
- Carry out inspections and periodic testing of lifting appliances and accessories as required by statutory legislation
- Advise our clients on the most suitable lifting equipment to meet their needs
- Fabricate bespoke attachments if none are readily available
- Carry out repairs and service on appliances, i.e. overhead cranes and lifting machines
- Supply any type of lifting appliance, accessory or attachment that is required.
Whether you own or operate lifting or hoisting equipment, you need to ensure that all items are safe, and in compliance with statutory requirements. That is where our specialist in-house inspection team can help. Our team can complete inspections at your site monthly, 3 monthly, 6 monthly or 12 monthly depending on the use and quantity of equipment. Whenever your inspection is due, which is automatically generated via our digital database management system, we will contact you to organise a suitable time for our inspector to be at your site. Our inspectors are fully trained to complete inspections and testing of all of your equipment.
All lifting gear has to be either inspected and/or tested in accordance with current legislation and best practice. The process of inspecting a unit is giving it a thorough inspection to check for any defects. If it passes, our crew fit a colour coded tag to it or coloured cable tie. The pass label indicates the date of inspection and next due inspection date. If it fails, we fit a red tag to it and remove it from service. We notify the owner and the current local enforcement authority. Testing the unit involves giving a thorough inspection first. If in good order we proceed with a proof load test of its safe working load plus a percentage above that depending on the type of equipment being tested. If it passes the load test, we inspect it again and issue a GA1 certificate.
How do we keep records and supply certification? After completing an inspection on site, a full equipment report, asset list and certificates (GA1) are issued to comply with the workplace health and safety requirements. All equipment inspected will be saved and electronically sent to the customer or alternatively can be accessed 24/7 through our Filemaker digital database management system.